Universal Testing Machines (UTMs) are essential in the world of material testing. They help determine the mechanical properties of various materials.
These machines are versatile, performing tests like tensile, compression, and bending. Engineers and scientists rely on UTMs for accurate data.
Understanding UTMs is crucial for quality control and product development. They ensure materials meet industry standards and perform as expected.
With advancements in technology, UTMs have become more precise and efficient. They are indispensable tools in many industries, from aerospace to construction.
This guide will explore the basics of UTMs, their components, and their applications.
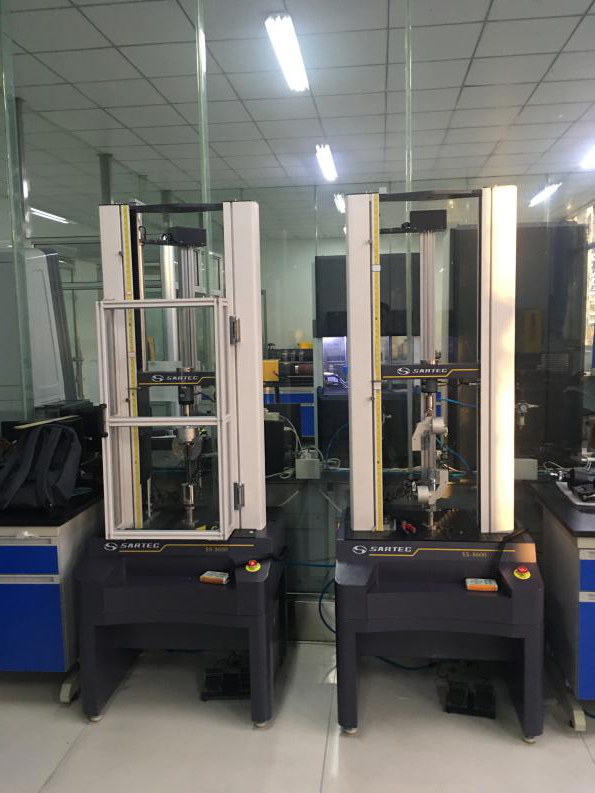
What is a Universal Testing Machine (UTM)?
A Universal Testing Machine (UTM) is a critical device used in material testing. It tests the mechanical properties of different materials under various conditions.
UTMs are versatile and capable of performing several types of tests. This includes tensile, compression, and bending tests, allowing for comprehensive material analysis.
The core purpose of a UTM is to apply controlled force to a material sample. It measures this force and the material’s response in terms of deformation.
Key Functions of a UTM:
Applying controlled forces
Measuring force and deformation
Evaluating mechanical properties
These machines are crucial for industries aiming to ensure product quality and reliability.
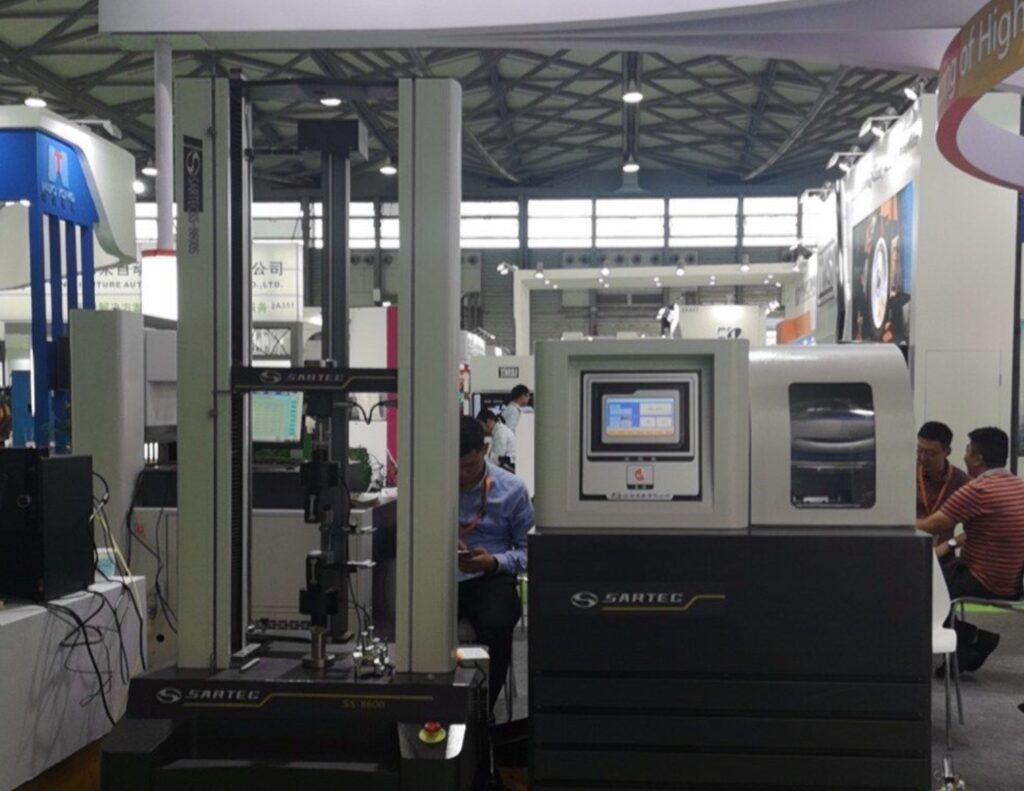
Key Components of a UTM
Understanding the key components of a Universal Testing Machine (UTM) is essential. Each part plays a crucial role in the machine’s operation.
The main components include the load frame, load cell, crosshead, and various test fixtures. These parts work together to ensure accurate testing.
UTMs have a load frame that provides structural support during tests. The load cell measures the forces applied, while the crosshead applies tension or compression.
Various grips, fixtures, and extensometers hold the specimen in place and measure elongation. Together, these elements ensure precise results.
Key Components of a UTM:
Load Frame
Load Cell
Crosshead
Grips, Fixtures, and Extensometers
These components are essential for the effective functioning of a UTM.
Load Frame
The load frame is the backbone of a UTM. It provides structural support and stability during tests.
This robust structure holds the test specimen and all testing components securely. Its design ensures accurate and reliable results.
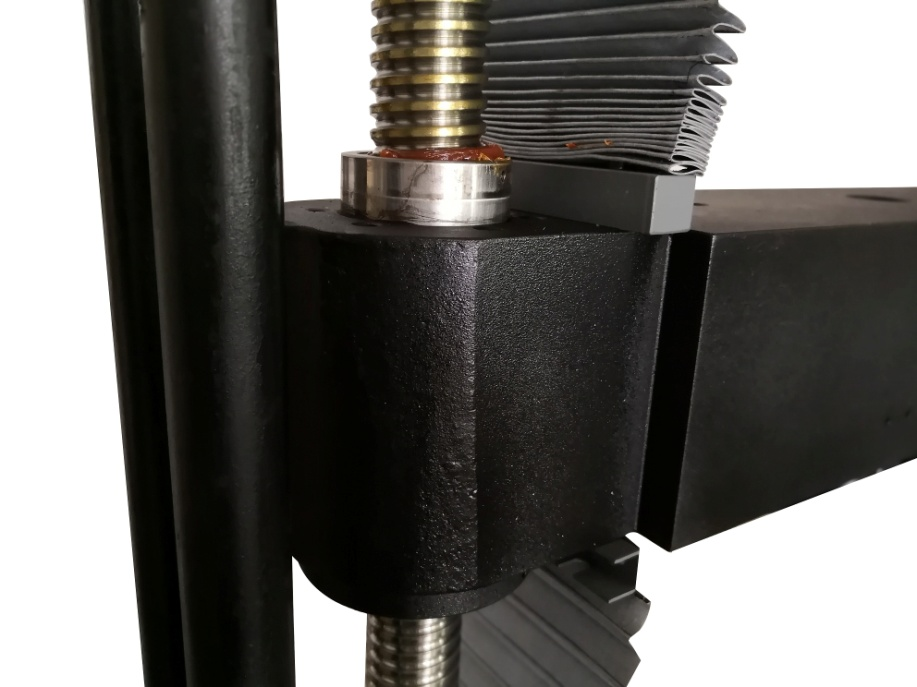
Load Cell
In a UTM, the load cell is vital for measuring applied force. It converts force into a measurable signal.
Load cells guarantee precision by offering accurate force measurements throughout the testing process. This ensures consistent results.
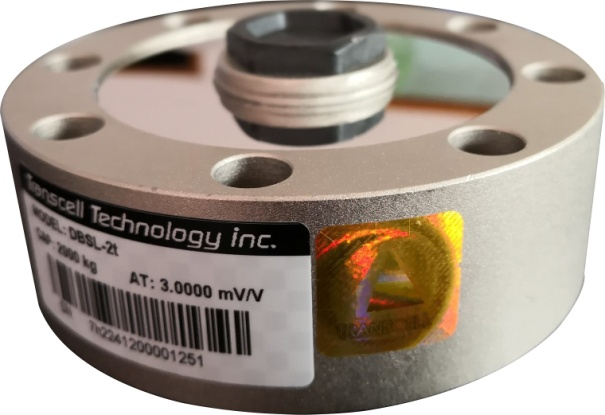
Crosshead and Actuator
The crosshead and actuator are central to applying force in UTMs. They move to apply tension or compression.
By adjusting the position of the crosshead, UTMs control the testing environment. This setup is crucial for reliable testing.
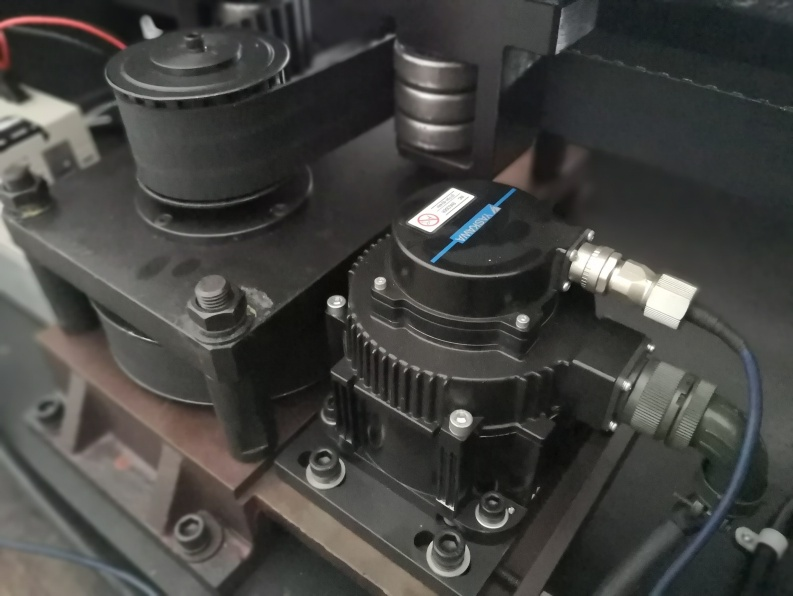
Grips, Fixtures, and Extensometers
Grips and fixtures secure the test specimen in place. They ensure stability and accuracy during testing procedures.
Extensometers measure the elongation of materials as force is applied. They provide valuable data on material deformation.
Types of Grips and Fixtures:
Mechanical grips
Pneumatic grips
Specialized fixtures
These tools, combined with extensometers, ensure precise and comprehensive material testing.
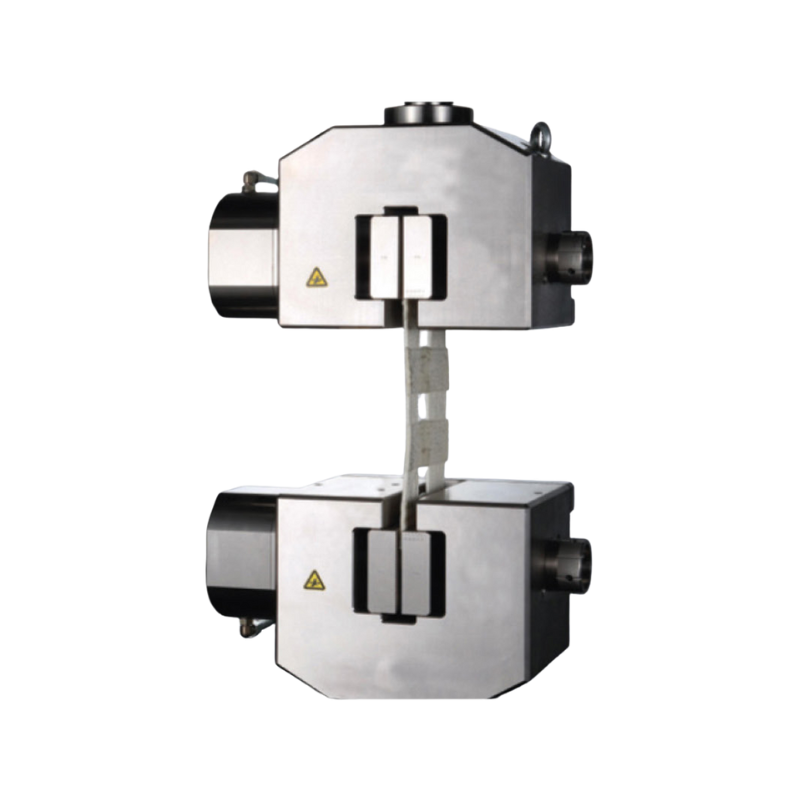
How Does a UTM Work? The Testing Process Explained
A Universal Testing Machine (UTM) operates through several organized steps. Each step contributes to precise and accurate material evaluation.
UTMs are designed to test materials in tensile, compression, and bending modes. The process involves preparing samples, applying forces, and recording data.
The UTM method is detailed and specific, ensuring meaningful results. It transforms raw material data into insights.
Each stage in the testing procedure is essential for understanding how materials behave. Understanding each step is crucial for success.
The UTM Testing Process:
Sample Preparation and Clamping
Applying the Force
Measuring the Response
Analyzing and Recording the Data
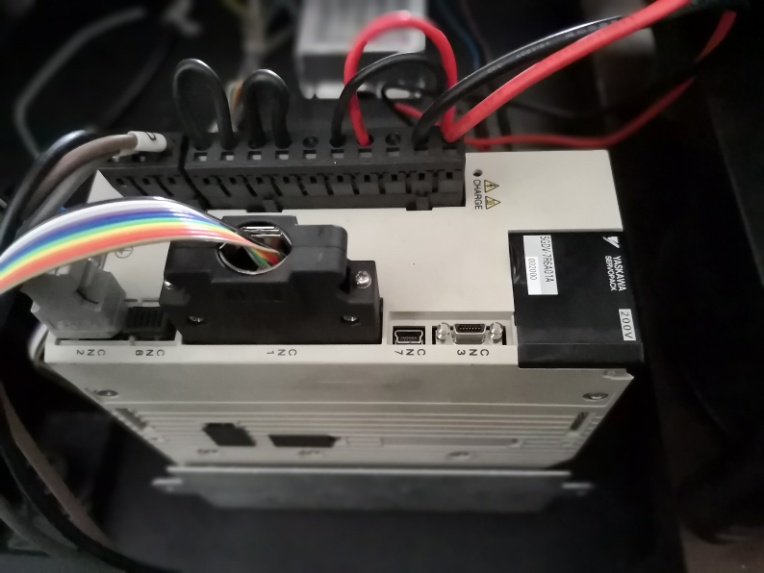
Step 1: Sample Preparation and Clamping
Sample preparation is the first critical step. The test specimen needs to be cut to precise dimensions.
Once prepared, the sample is clamped securely in the UTM. This ensures stability during the test procedure.
Step 2: Applying the Force
The next step involves applying a controlled force. The UTM uses the crosshead and actuator to apply tension or compression.
This phase is methodical, gradually increasing the load. The process simulates real-world mechanical stress conditions.
Step 3: Measuring the Response
As the force is applied, the material’s response is measured. The UTM monitors changes in length, deformation, and load.
This real-time data collection provides invaluable insights. Variations in material properties are captured during this phase.
Step 4: Analyzing and Recording the Data
Finally, the collected data is analyzed and recorded. UTMs use sophisticated software to generate detailed reports.
The analysis determines key mechanical properties. Results include stress-strain curves and critical load points.
Important Analysis Outputs:
Stress-strain data
Yield strength
Ultimate tensile strength
The results are stored for further evaluation. This data drives improvements and innovations in material science.
Types of Tests Performed by UTMs
Universal Testing Machines can perform several vital tests to evaluate material properties. Each test type reveals unique attributes of the material.
Common Tests with UTMs:
Tensile Testing
Compression Testing
Bending and Flexural Testing
These tests help in understanding material strength and flexibility. The insights gained are crucial for quality control.
Testing types accommodate various industrial needs. Selecting the appropriate test ensures accurate assessments.
Tensile Testing
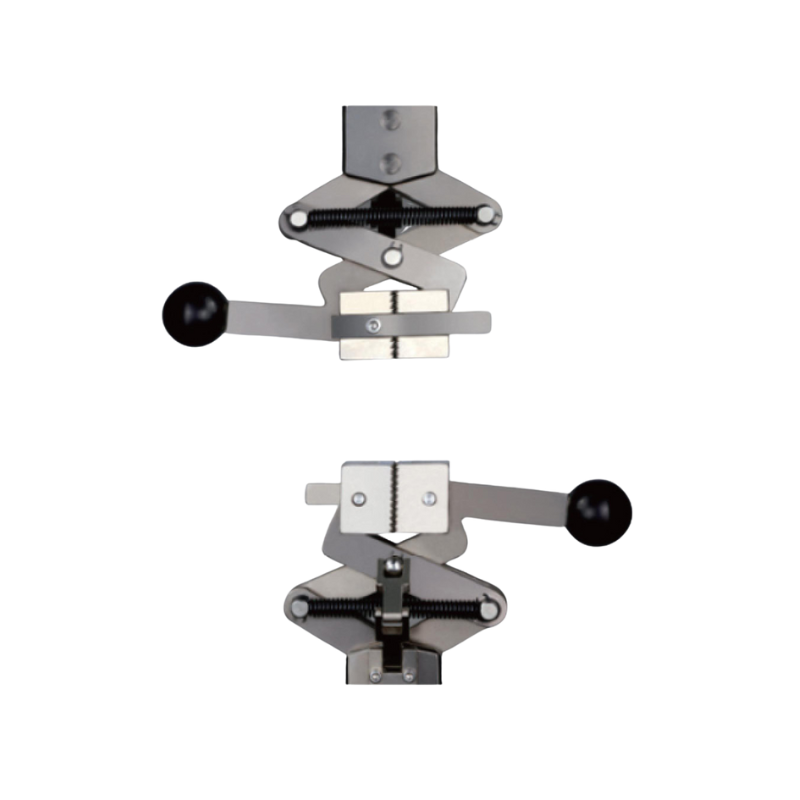
Tensile testing measures how materials stretch when pulled. The test provides data on elongation and breaking point.
This test helps identify tensile strength and elasticity. Engineers rely on this test to forecast material performance.
Compression Testing
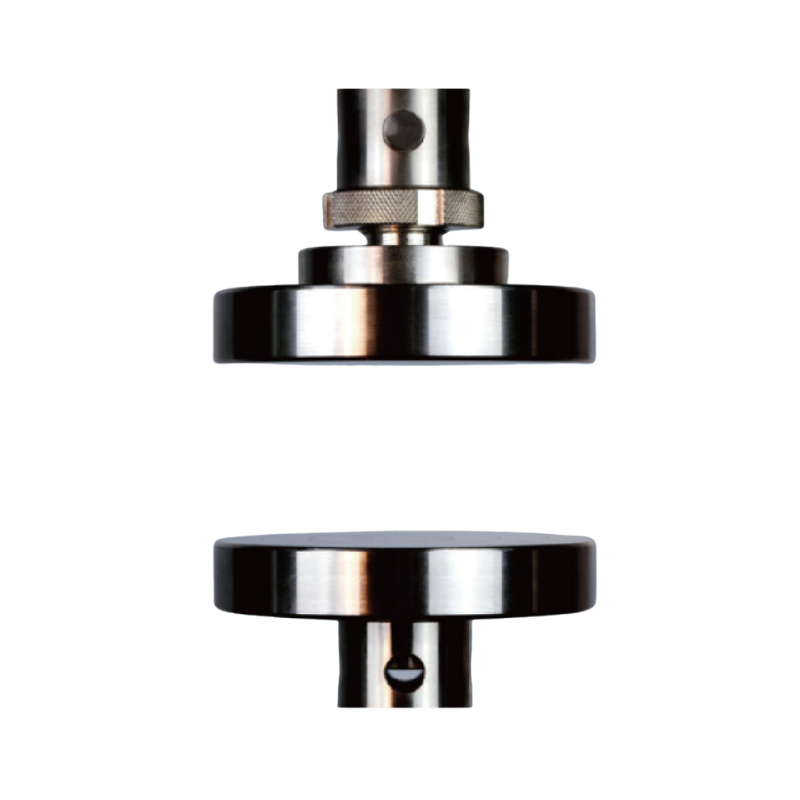
Compression testing examines material behavior under squeezing forces. It evaluates how much load a material can withstand.
This test is vital for materials used in construction. Understanding compression strength prevents structural failures.
Bending and Flexural Testing
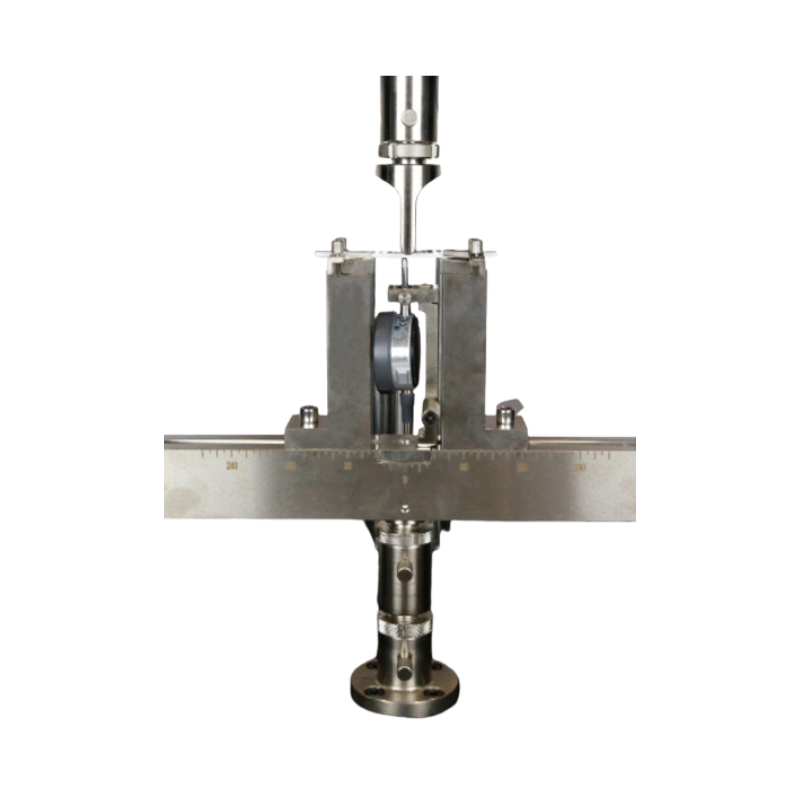
Bending tests assess material flexibility and resistance. Flexural strength indicates how well a material can bend without breaking.
These tests help in determining material suitability for load-bearing applications. Flexural tests are critical for materials like plastics and wood.
Applications of Universal Testing Machines
Universal Testing Machines find applications across numerous industries. They play a crucial role in quality assurance and research.
Common Applications:
Aerospace
Automotive
Construction
Manufacturing
In aerospace, UTMs ensure materials meet strict safety standards. They’re vital for testing high-performance components.
The automotive industry uses UTMs for crash simulation and safety analysis. They help develop more resilient vehicles.
In construction, UTMs assess the strength of building materials like steel and concrete. They guarantee structural integrity.
Manufacturers employ UTMs to refine product durability, ensuring consistency and reliability.
Every industry relies on UTMs to verify material performance, making them indispensable tools in development and quality control.
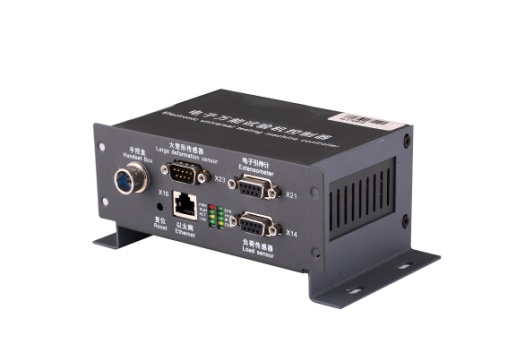
Importance of UTM Test Data in Industry
Universal Testing Machine (UTM) test data is vital for ensuring the safety and performance of materials. Industries rely on this data to maintain quality and meet standards.
Key Benefits of UTM Test Data:
Enhances product design
Validates material specifications
Supports regulatory compliance
Informed decisions can be made with accurate UTM test data. Engineers and developers use this information to refine and improve products, ensuring customer satisfaction and safety. Without reliable data, predicting material behavior becomes a significant challenge, risking project viability and safety.
Choosing the Right UTM for Your Needs
Selecting the appropriate Universal Testing Machine (UTM) involves understanding your specific testing requirements. Different industries and applications demand varying UTM capabilities.
Key considerations when choosing a UTM include:
Test types (tensile, compression, bending)
Material types and sizes
Load capacity and accuracy
Assess the features you need, including digital interfaces and environmental testing capabilities. Consider the adaptability of the UTM to future testing needs. Selecting a flexible and accurate machine ensures comprehensive material testing. Correctly assessing these factors will enhance testing efficiency and reliability.
Maintenance, Calibration, and Safety Considerations
Proper maintenance of Universal Testing Machines is crucial for accurate results and long-term operation. Regular maintenance helps in identifying wear and ensuring that all parts function correctly.
Calibration is essential for reliable test outcomes. It must be performed routinely to verify the precision of the measurements. Regular calibration also helps maintain compliance with industry standards and enhances test reliability.
Safety is paramount when operating UTMs. Always follow recommended safety protocols, which include:
Ensuring all guards are in place
Using appropriate personal protective equipment (PPE)
Regular inspection for any faults or damage
Prioritizing these aspects reduces the risk of accidents and equipment malfunction, ensuring a safe and efficient testing environment.
by Ratapan Anantawat (https://unsplash.com/@rtp_atw)
The Evolution and Future of Universal Testing Machines
Universal Testing Machines have seen significant advancements since the early 20th century. Initially mechanical, they are now highly automated with digital interfaces. This evolution has increased precision and expanded their application range.
The future looks promising with ongoing innovations. Emerging technologies like artificial intelligence and machine learning might further revolutionize testing processes. These advancements promise to enhance efficiency and provide deeper insights into material properties.
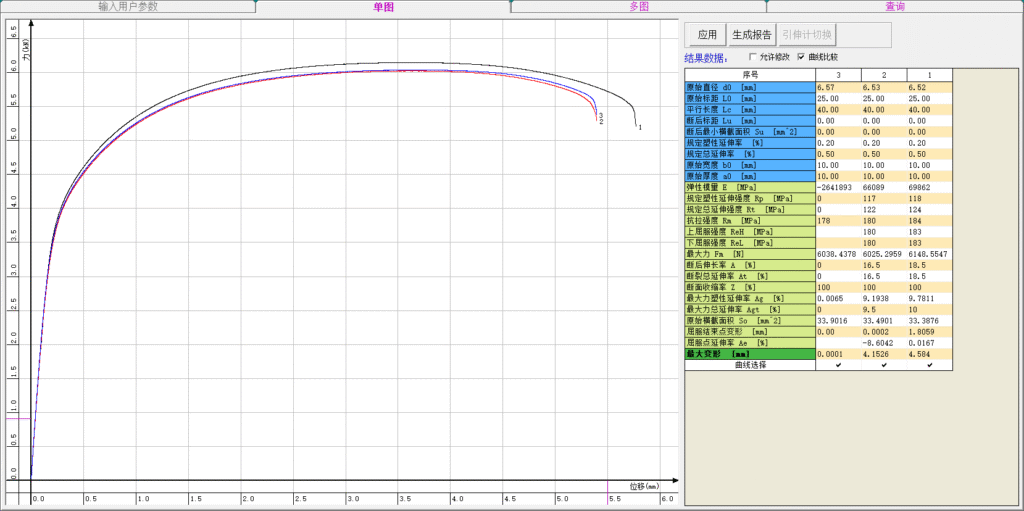
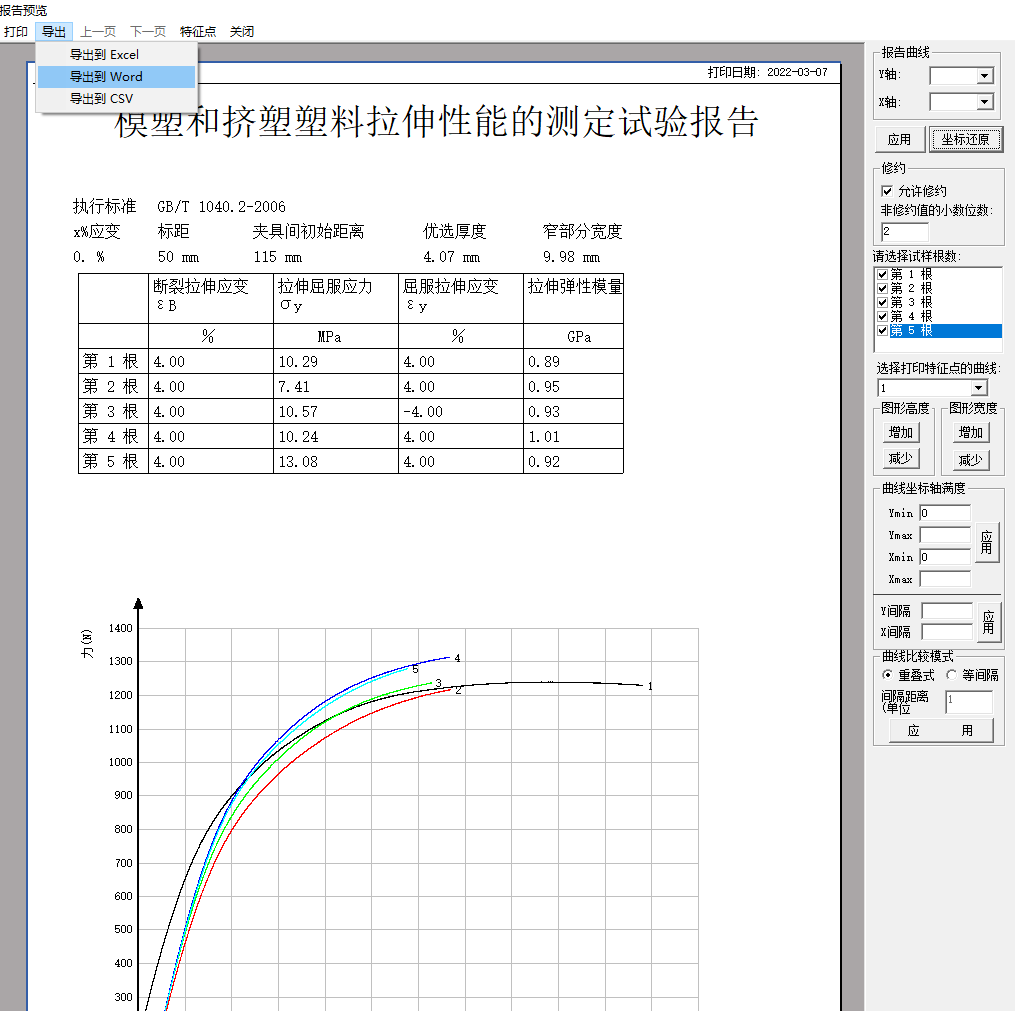
Conclusion: Why Understanding UTMs Matters
Understanding Universal Testing Machines is crucial for anyone involved in material testing and quality control. Their versatility and precision make them indispensable for developing safer, more reliable products. Knowledge of UTMs enables effective material testing and innovation across industries.
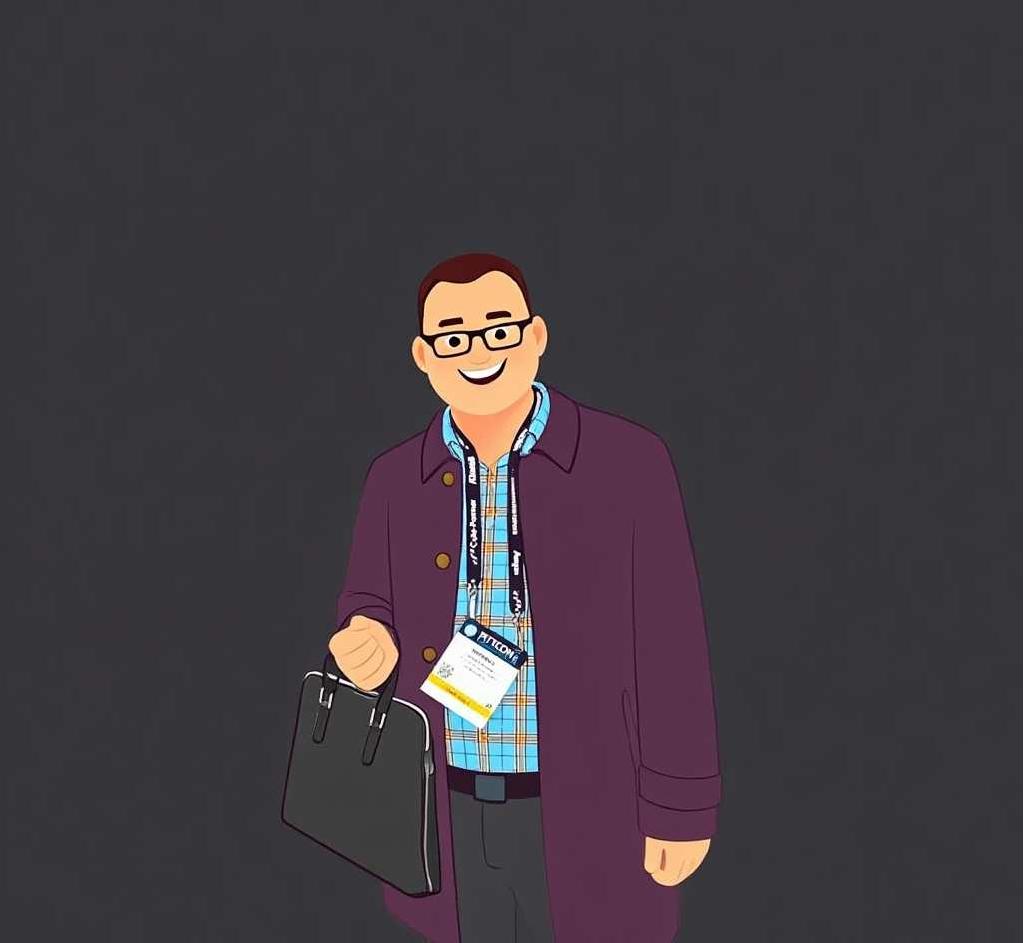